Introduction to Robotic Actuators
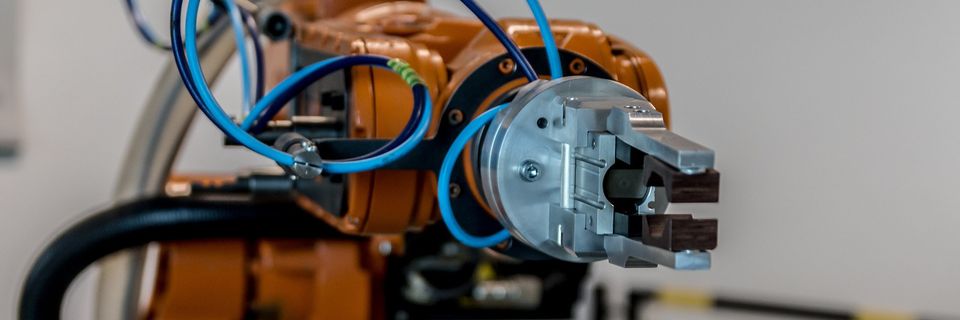
Robotic actuators are electromechanical devices that do some kind of physical task. They range in size from small consumer products to immense industrial equipment. Most robots contain multiple actuators.
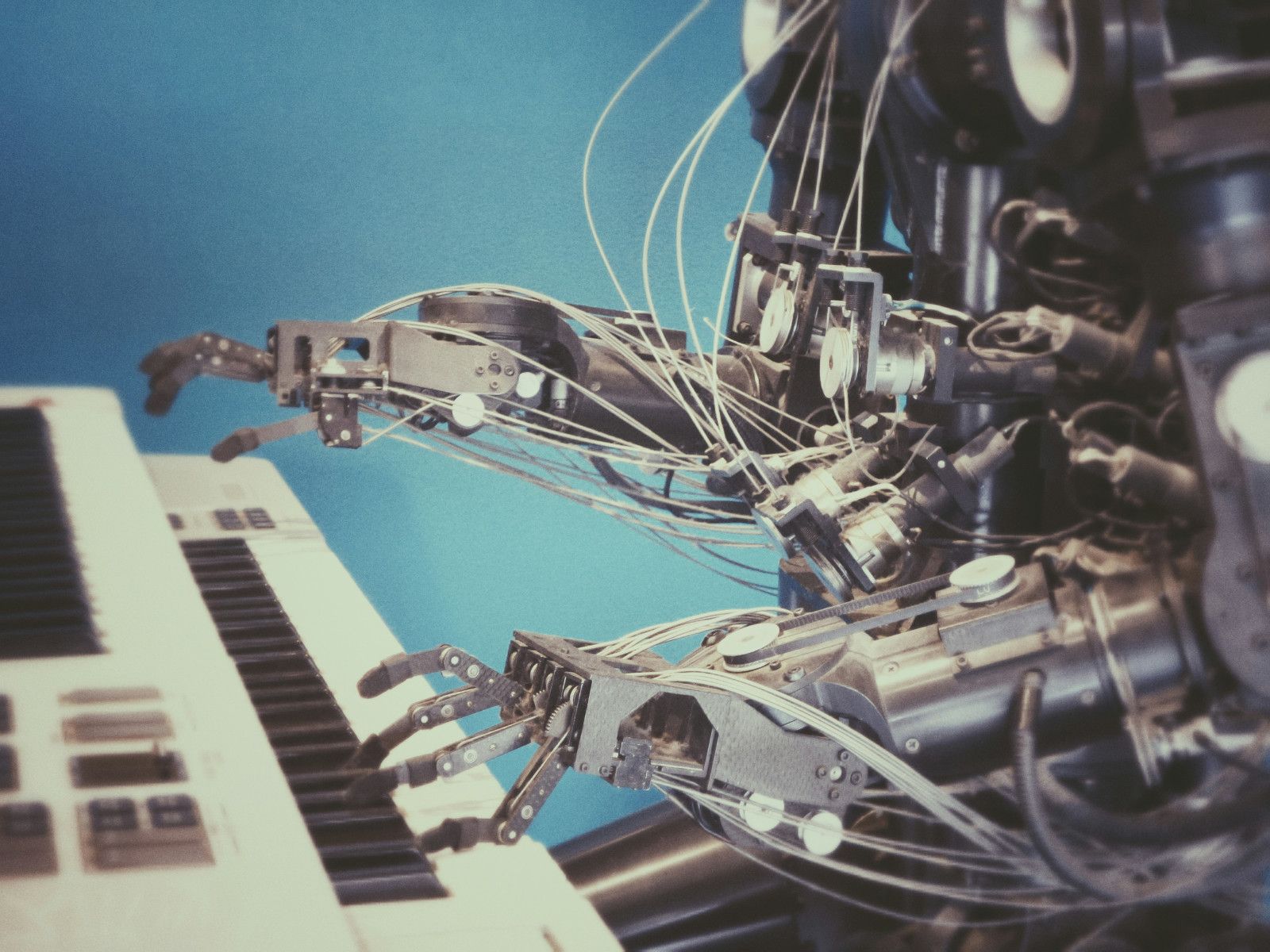
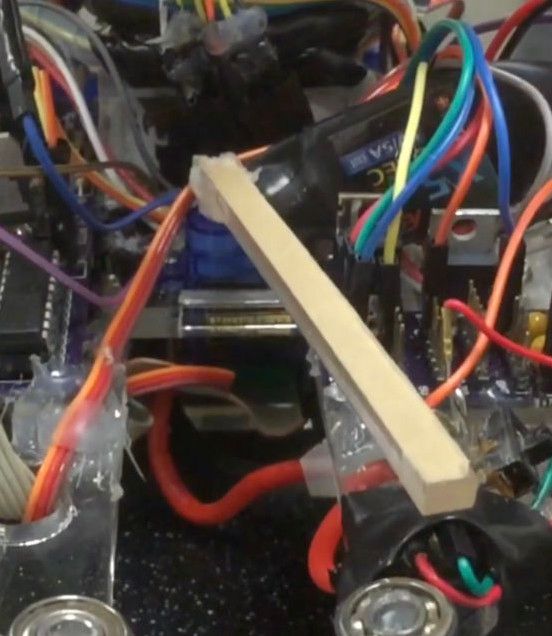
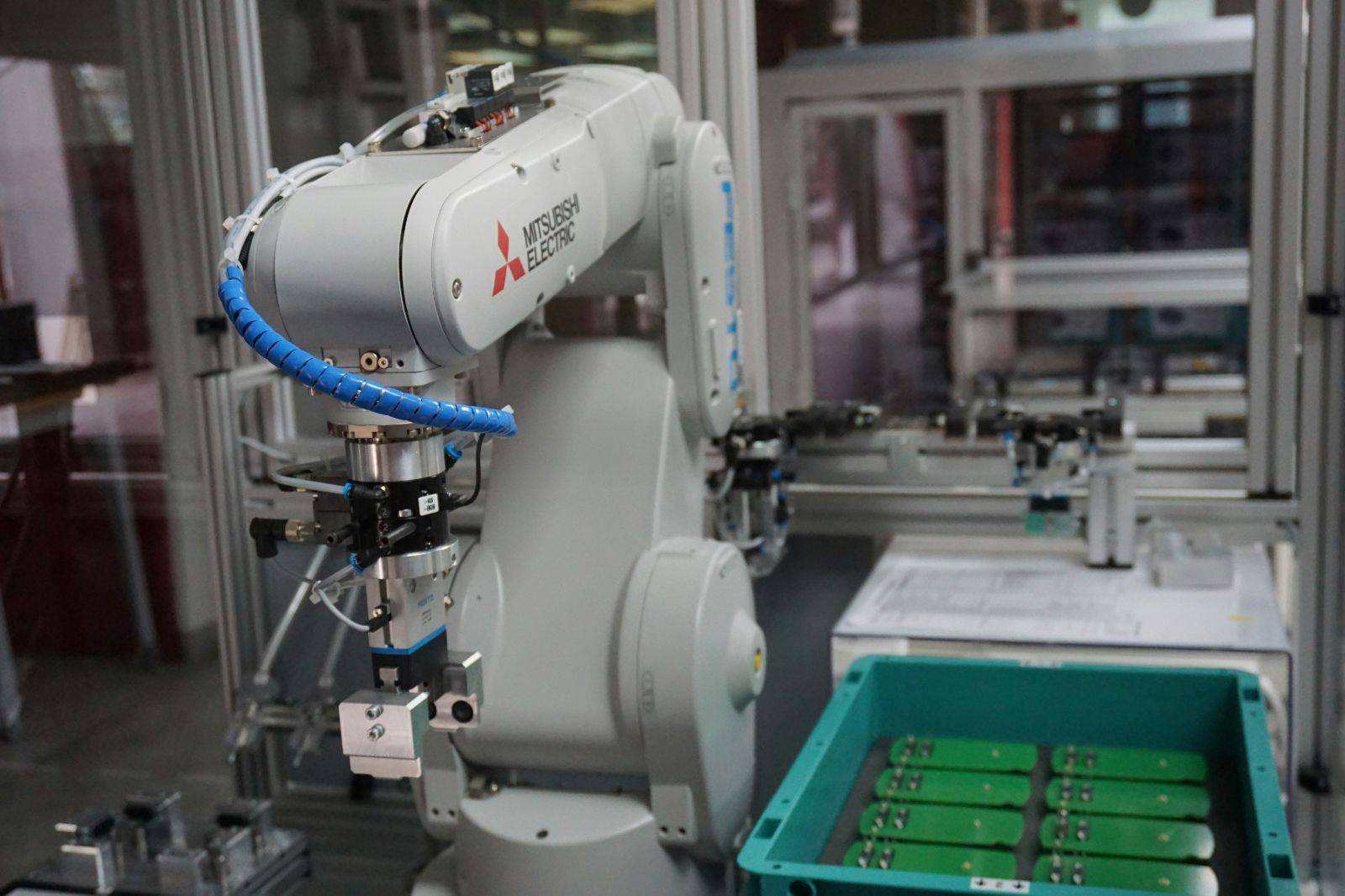
Figure 1:Left- Robot playing piano, courtesy of Possessed Photography via Unsplash | Center- Light break actuator | Right- Mitsubishi robot arm, courtesy of Patricio Davalos via Unsplash
A robotic actuator is a simple composition of smaller components.
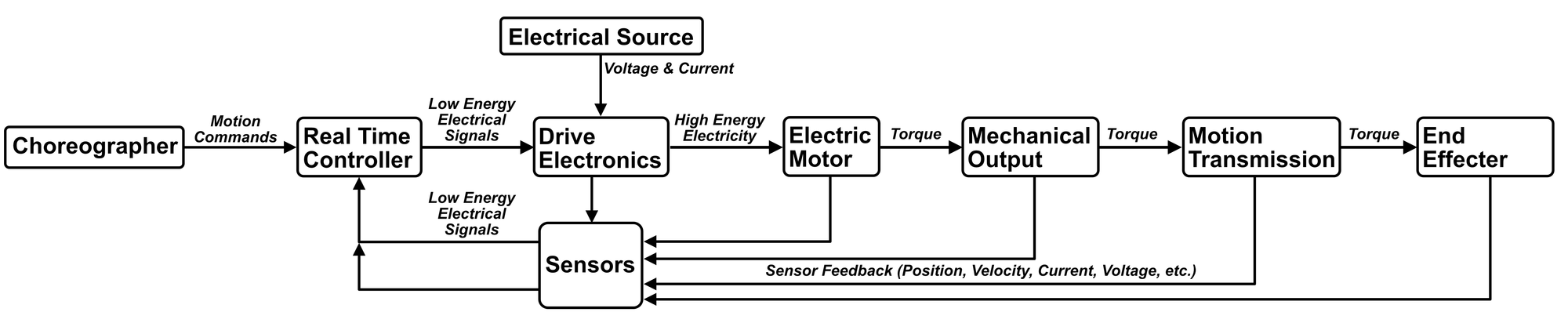
Okay... maybe not so simple. There's actually a lot involved in building an actuator. Required knowledge includes mechanics, electronics, programming, control systems, metrology, and more. Even for those who possesses the knowledge, every actuator is different. The myriad of different applications, operating systems, microcontrollers, motor technologies, sensor types, etc. make each robotic actuator challenging to design and integrate. Actuators are often designed by entire teams of engineers, each specialized in one core area of the actuator.
Choreographers
A choreographer composes actions and motions to achieve a high level objective, generally by orchestrating synchronous motion of multiple actuators.
The pervasiveness of video game controllers and high speed computing devices have made choreography equipment easy to obtain. The device you are reading this article on right now is likely a capable choreographer. Choreographers are often a combination of human input and software.
Live Choreographer
Human interface controllers allow direct control of a robot's motion through buttons, knobs, triggers, and other inputs. A human can choreograph as many actuators as their dexterity and cognitive abilities allow. RC vehicles (drones, planes cars, etc.) and Hollywood animatronics are often controlled through live choreography.

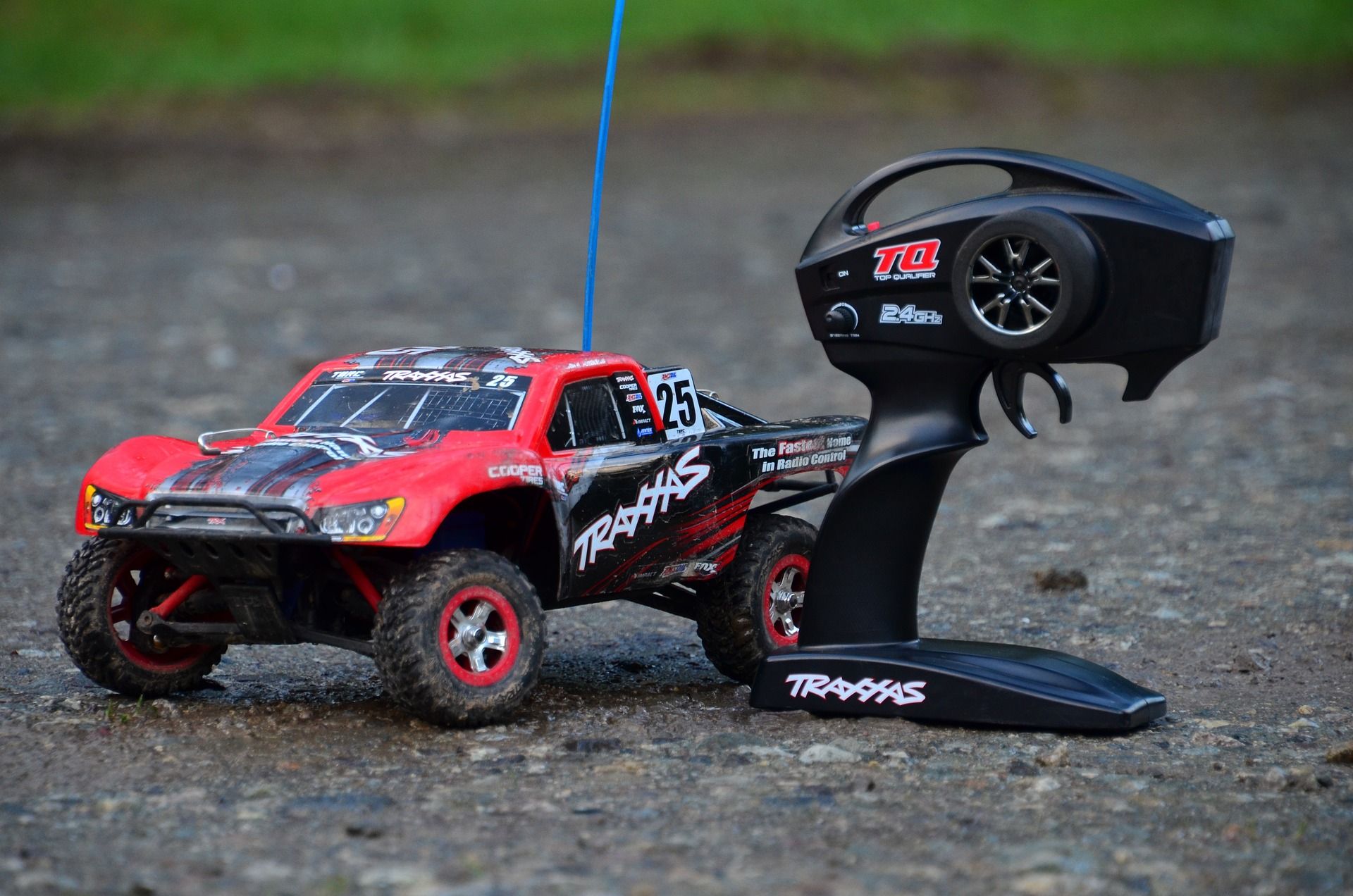
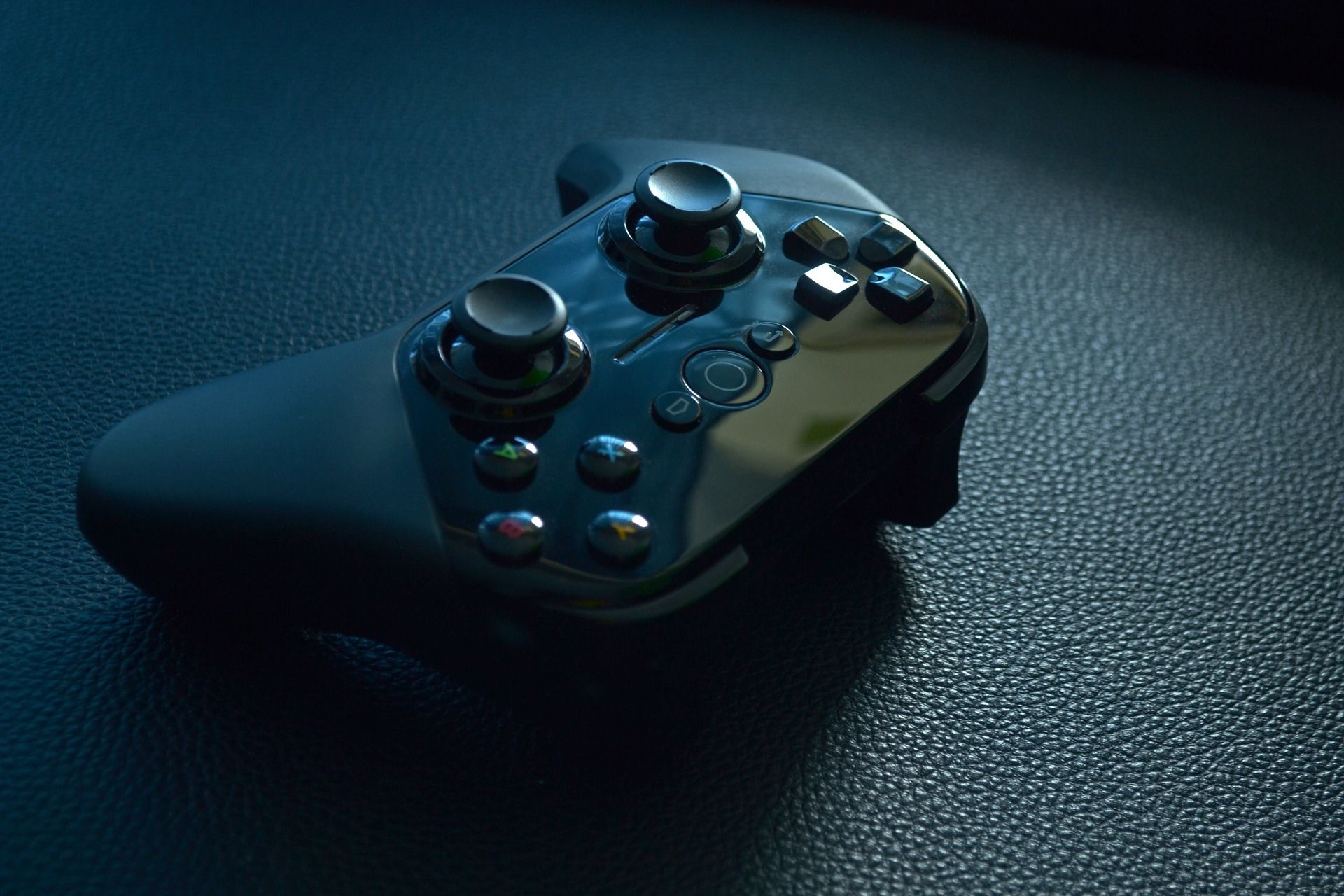
Figure 3:Left- Drone controller, courtesy of Austin Pacheco via Unsplash | Center- Radio control car with remote, courtesy of Trevor205 via Pixabay | Right- Wireless game controllers can often be repurposed for controlling robots, courtesy of Quakeboy via Pixabay
Figure 4: Youtuber James Bruton has built a live controller for animatronic eyes using joysticks.
Precomputed Choreographer
Precomputed choreographers allow for preparing coordinated motion of multiple axes in advance. They are often coupled with kinematic simulators to show a preview of the motion to be performed. Because the motion is precomputed, it can be iteratively tuned for very precise motion. CNC milling machines, laser cutters, 3D printers, and looped animatronics are often controlled through precomputed choreographers.
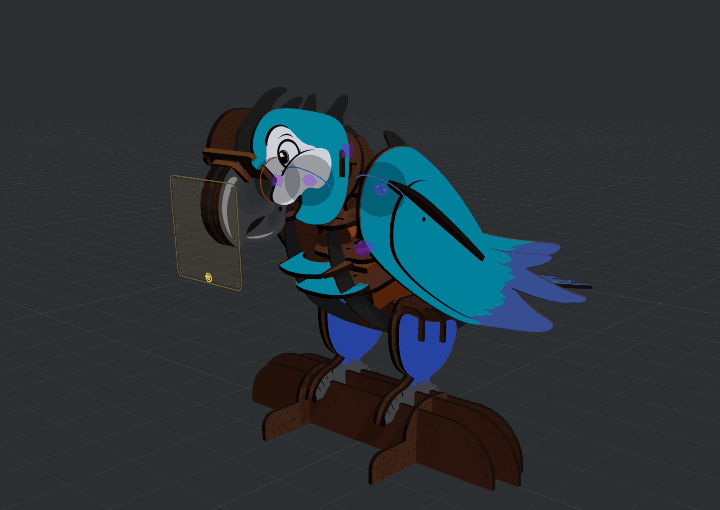
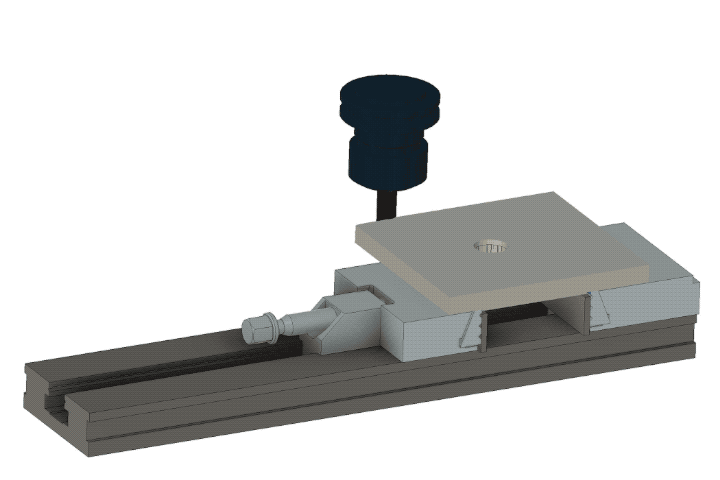
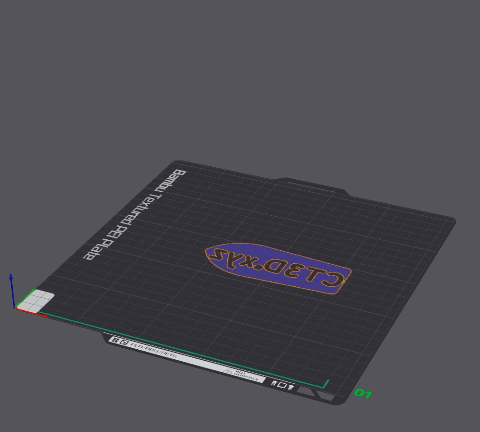
Figure 5:Left- Bottango is an animatronic choreography application for all major desktop operating systems | Center- Fusion 360 is an engineering application that can be used to choreograph machining tool paths | Right- Slicing software for 3D printers can be used to choreograph 3D printers
Dynamic Choreographer
Dynamic choreographers generate motion dynamically in response to sensor inputs or information from other robots. Modern dynamic choreographers are often coupled with advanced simulations (digital twins) to validate the robot's response in different environments.
Figure 6: NVIDIA has used digital simulations to make incredible advancements in robotic control technology.
Figure 7: A dynamically controlled robot that uses sensory inputs to accomplish a set of tasks to complete an overall objective. This robot was constructed by myself and fellow students during our undergraduate coursework.
Real-Time Controllers
Real-time controllers must maintain precise time keeping and synchronization to ensure that all actions commanded by the choreographer are performed at the correct time.
In early robots, Programmable Logic Controllers (PLCs) and electrical circuits were used to perform real time functions. PLCs are high-end controllers designed specifically for industrial automation; they cost hundreds to thousands of dollars. Electrical control circuits aren't terribly expensive but take a lot of specialized knowledge to design correctly.
Today, cheap, highly capable digital microcontrollers permeate the industry. An electronic chip smaller than a dime can replace what used to be an entire cabinet of electronics. They can be purchased off the shelf in low quantities for just a few dollars.
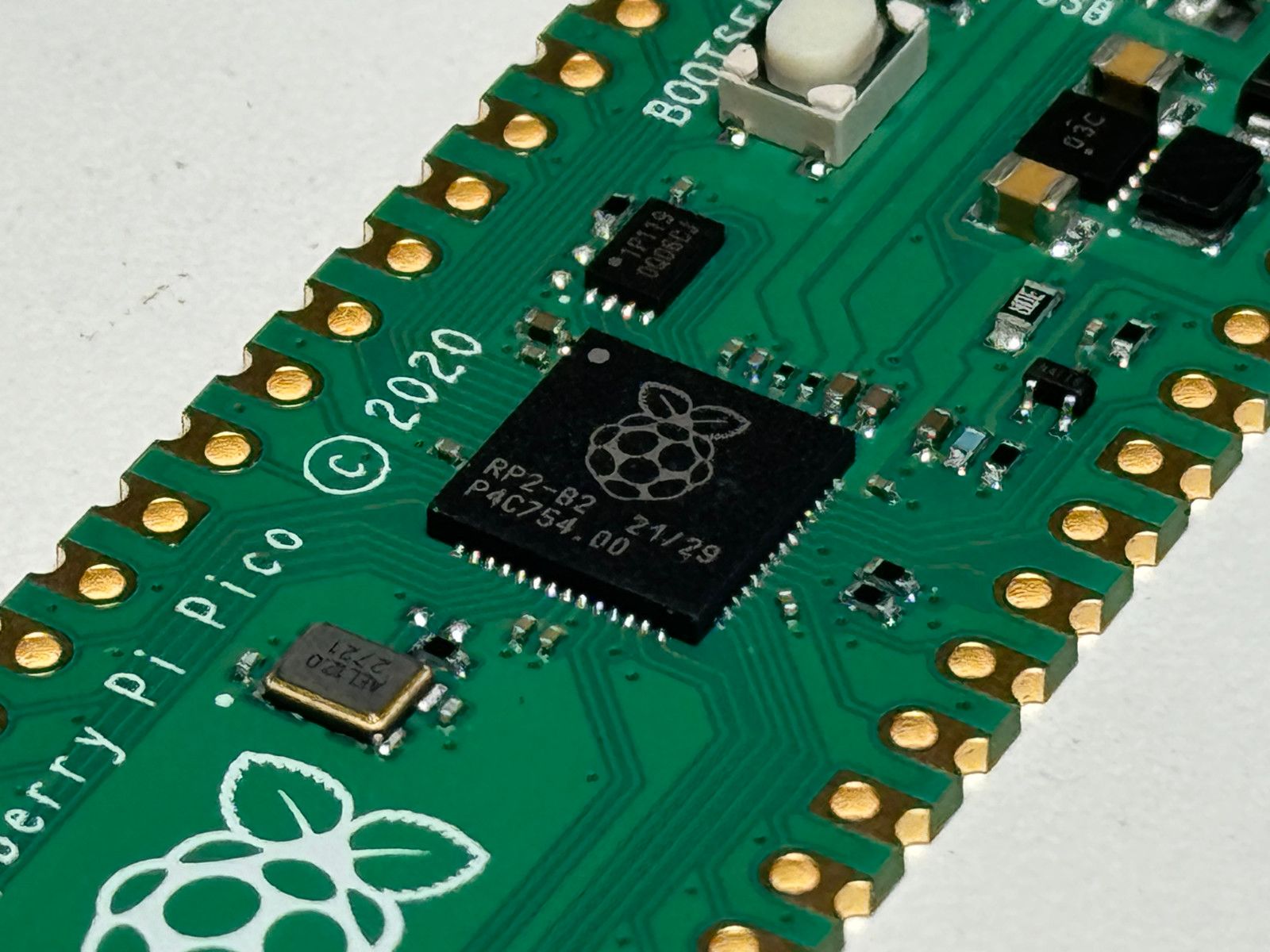
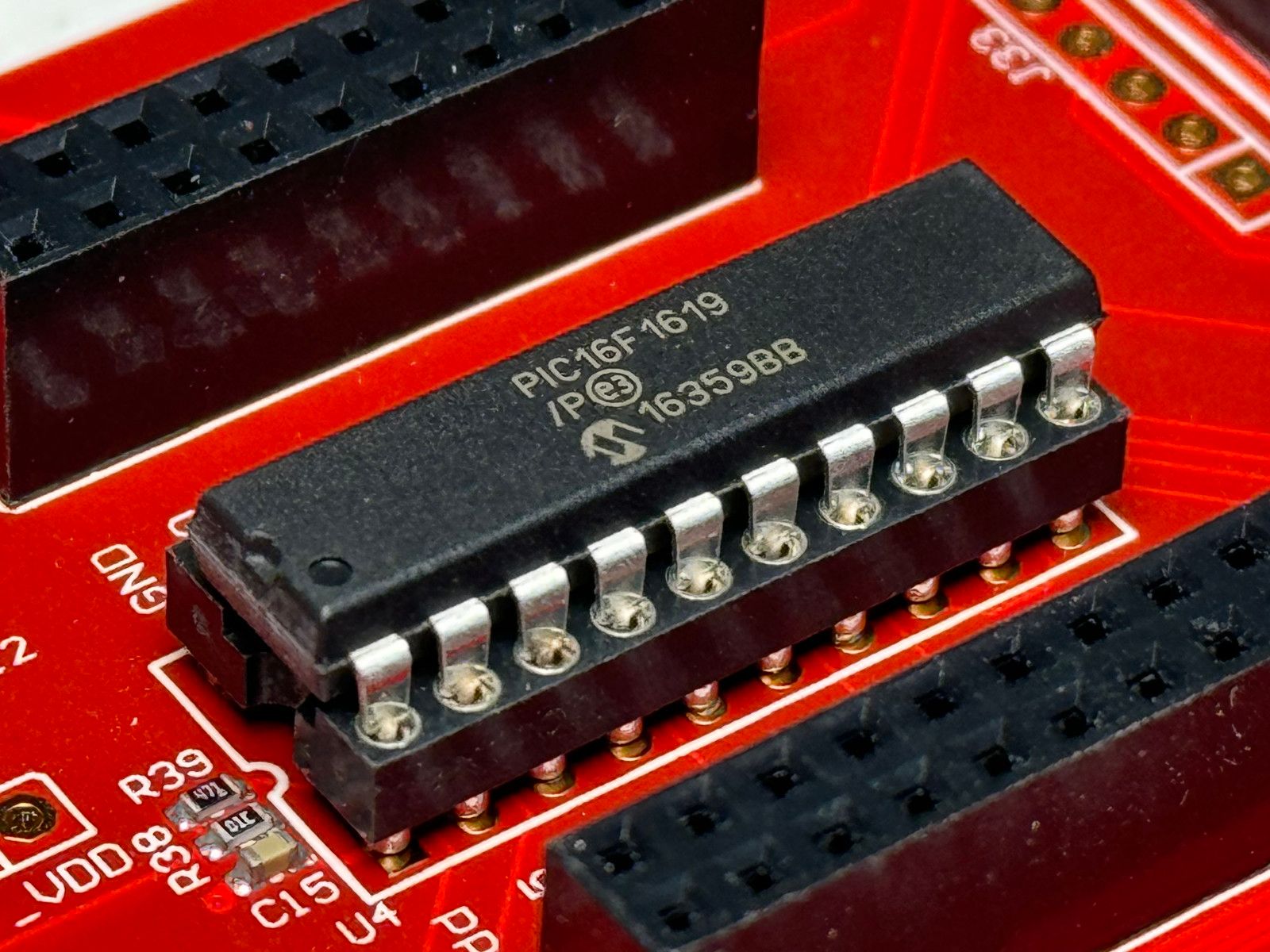
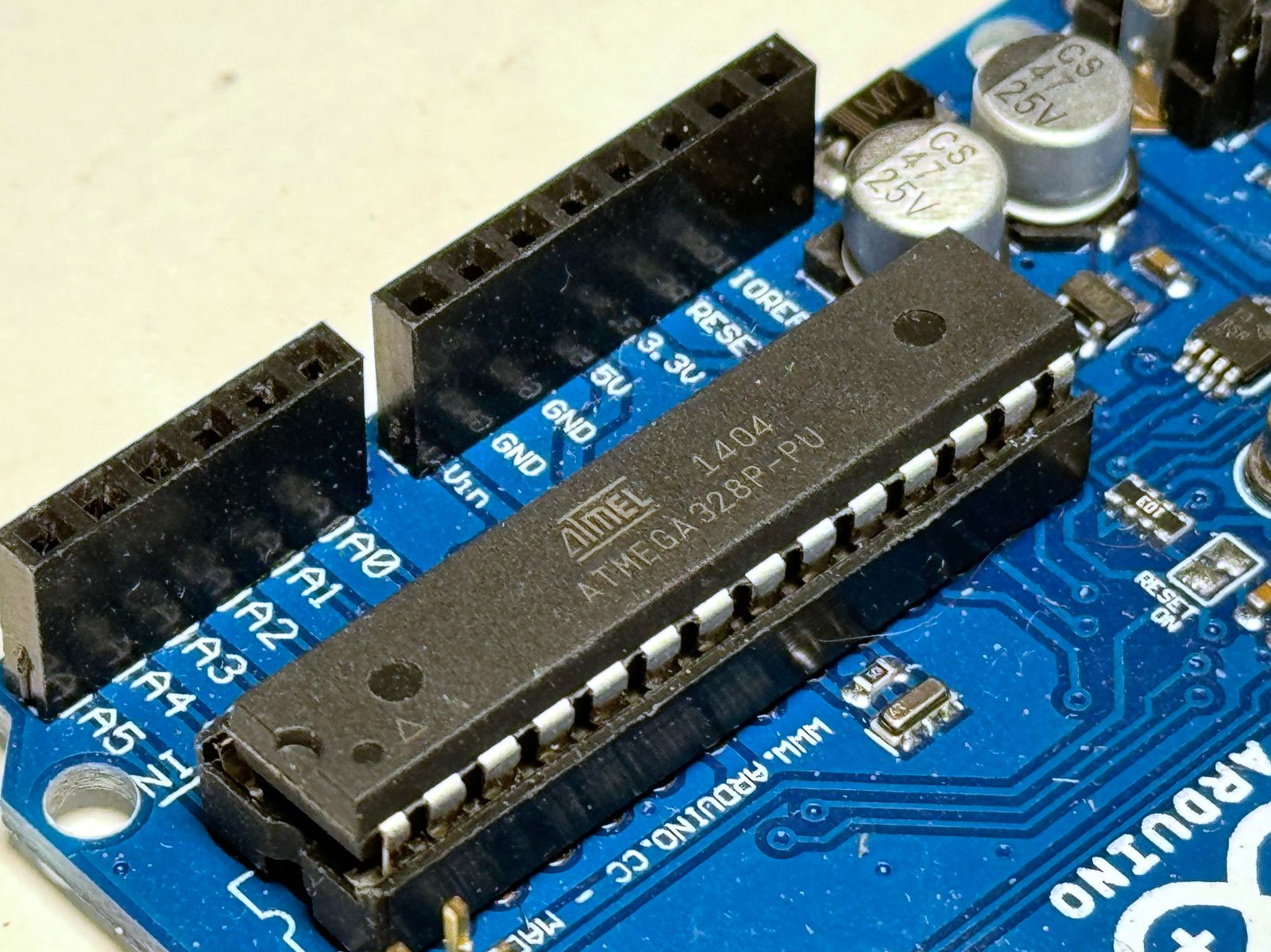
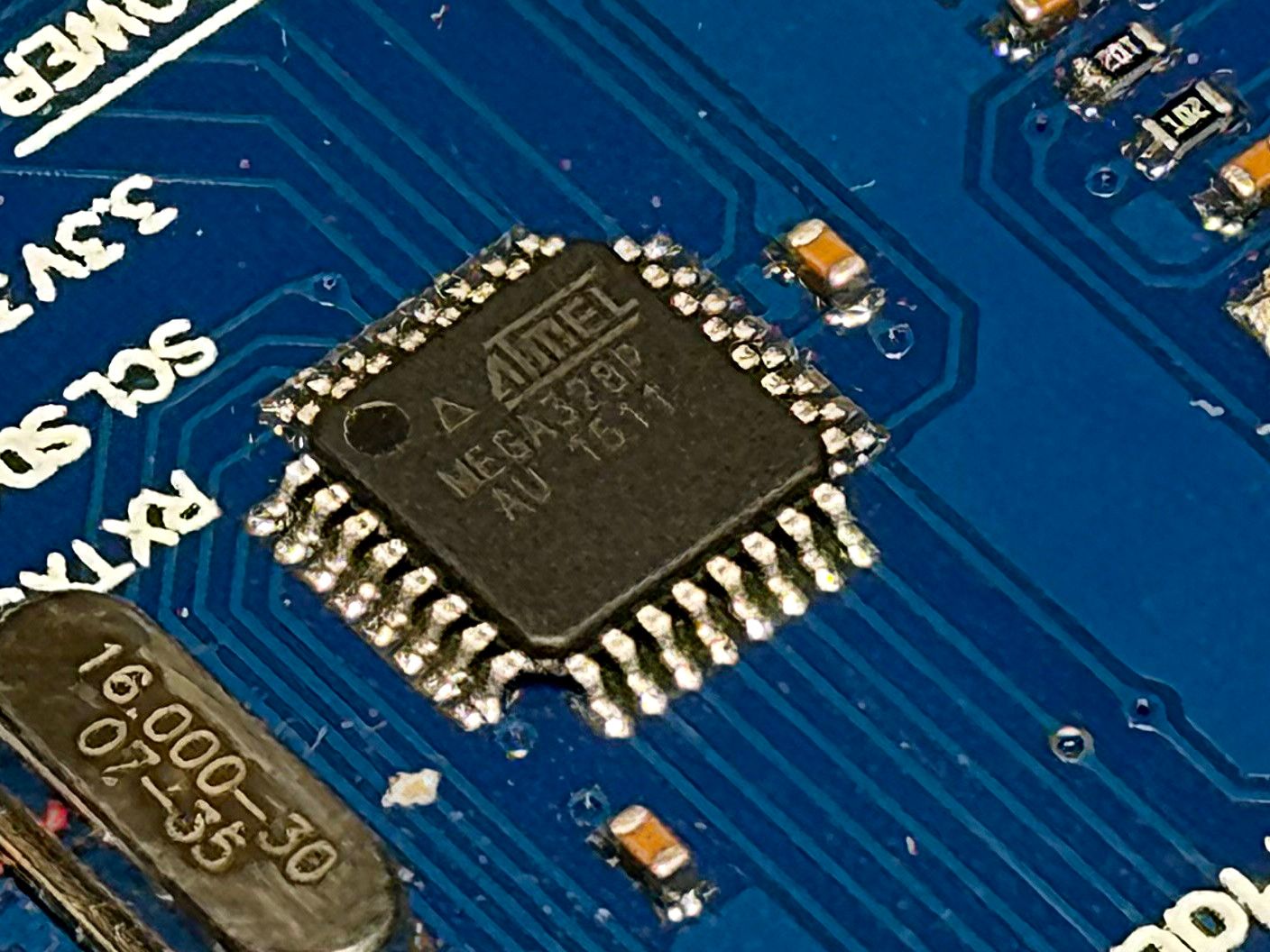
Figure 8:Upper Left- The RP2040 is a tiny, surface mount dual-core 32-bit microcontroller | Upper Right- The PIC family of microcontrollers from Microchip remains one of few brands to continue to release products in DIP (Dual In-line Package). Because the DIP form factor is through hole, it is very easy to solder though not very space efficient. | Lower Left- The original Arduino board has a removable 8-bit ATMEGA328P. The board could be used in a prototype and then the microcontroller could be removed and soldered to a new board. | Lower Right- The ATMEGA328P controller is also available in a small footprint surface mount chips
Drive Electronics
An electric motor typically requires a higher voltage than the real-time controller. The drive electronics use the controller's low voltage signal to control the motor voltage. The drive electronics are also designed to meet a motor's high current draw.
All motors must have their voltage switched within the motor's coils; this is called commutation. Brushed motors do this through mechanical means while brushless motors require advanced drive electronics to perform this task.
Electrical Sources
A motor and controller cannot be simply plugged straight into the wall. The wall voltage needs to be converted for the controller and motor by a power supply. The power supply needs to supply enough current for both. Common power supplies are intended for phones and computers... not robotic actuators. Power supplies come in all shapes and sizes, each with different features and drawbacks.
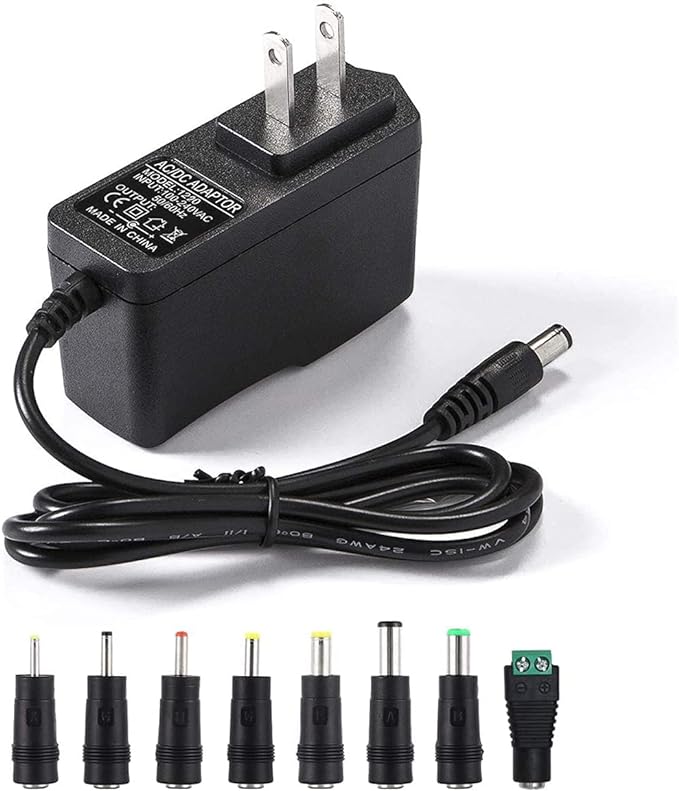
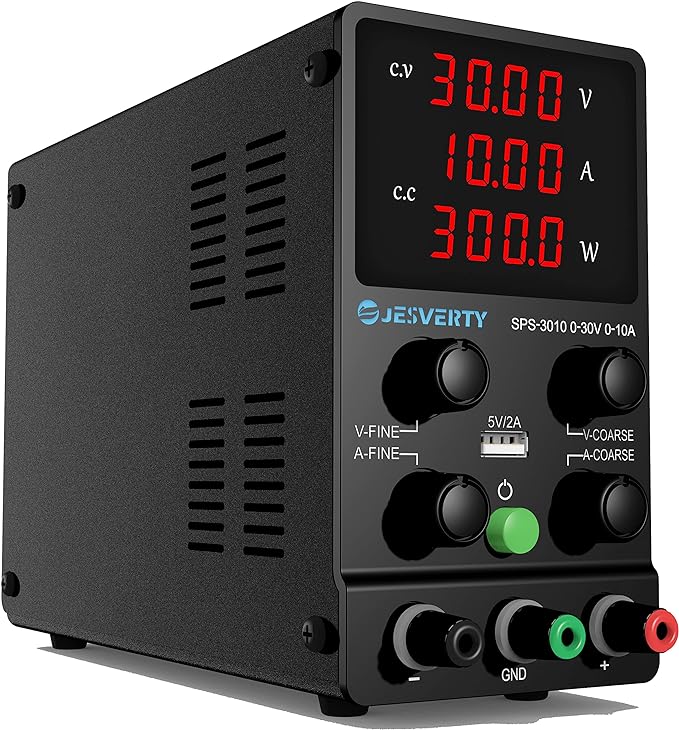
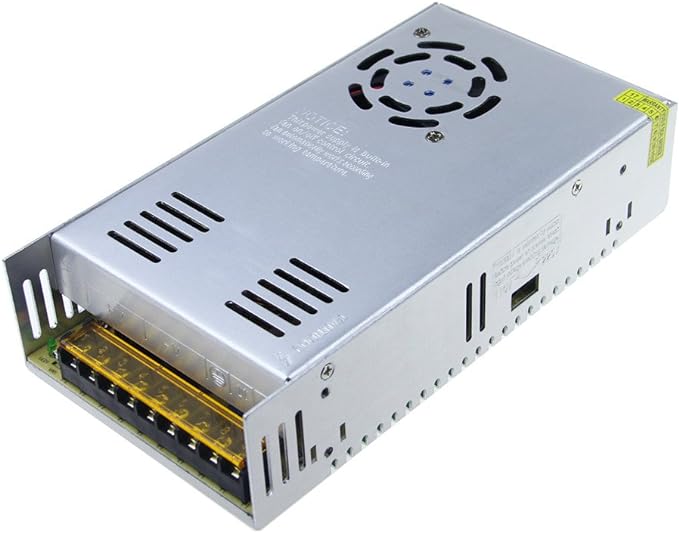
Figure 9: Electrical sources come in many different form factors. The examples shown here are representative but not associated with or recommended by mechatronics.studio. | Left- AC\DC Adapters are convenient but provide low current and typically only have one plug. Courtesy of Litstar | Center- Variable voltage power supplies allow for adjustment of current and voltage, however, their physical knobs make them susceptible to tampering (accidental and intentional). Courtesy of Jesverty | Right- Large switching power supplies have a lot of current capacity and many output terminals, however, they have exposed high voltage terminals that must be treated responsibly. Courtesy of Alitove.
Electric Motors
Electric motors convert electrical current to mechanical torque. There are many kinds of motors, differing in their form factors, speed/torque capabilities, and price points.
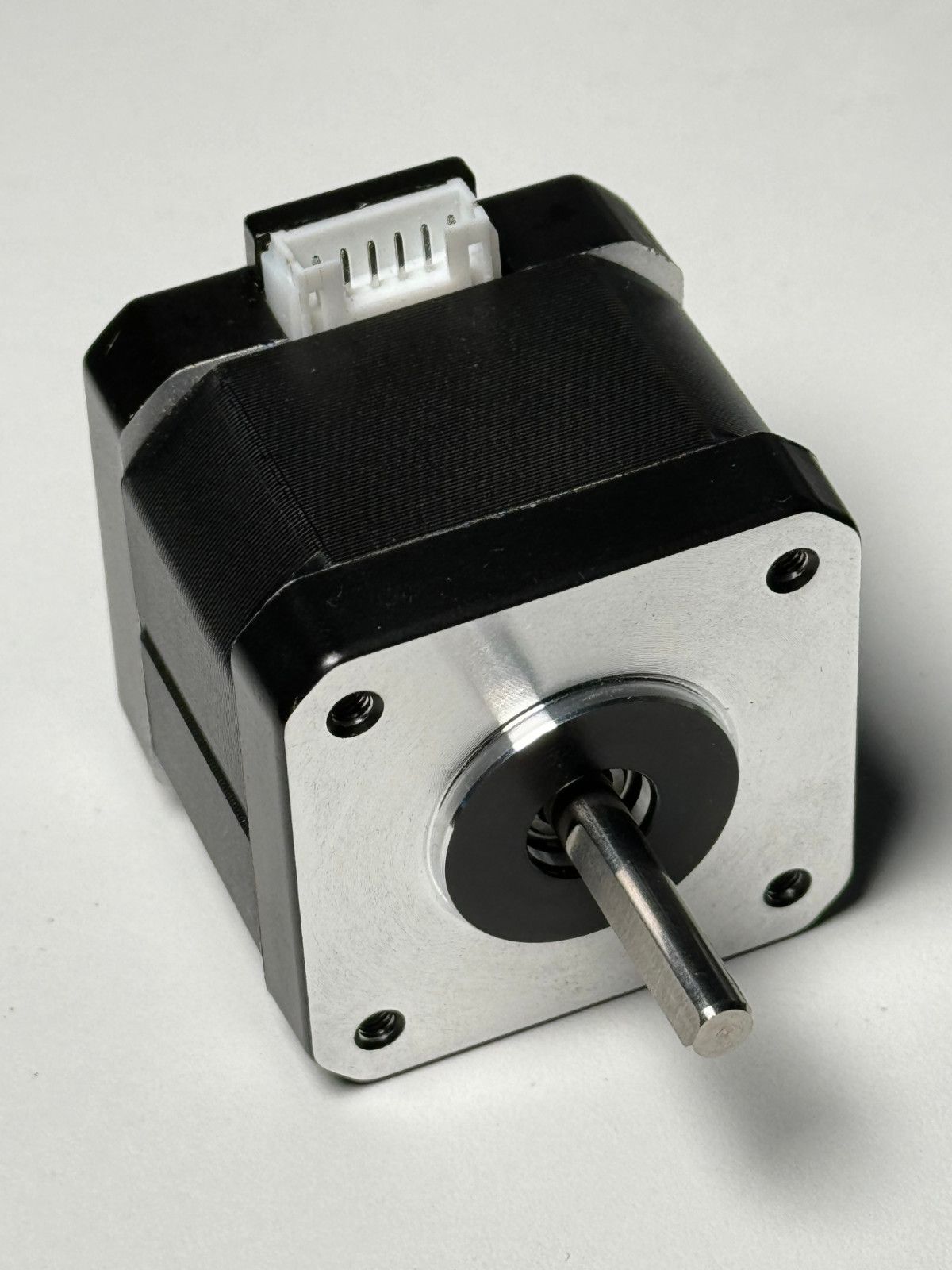
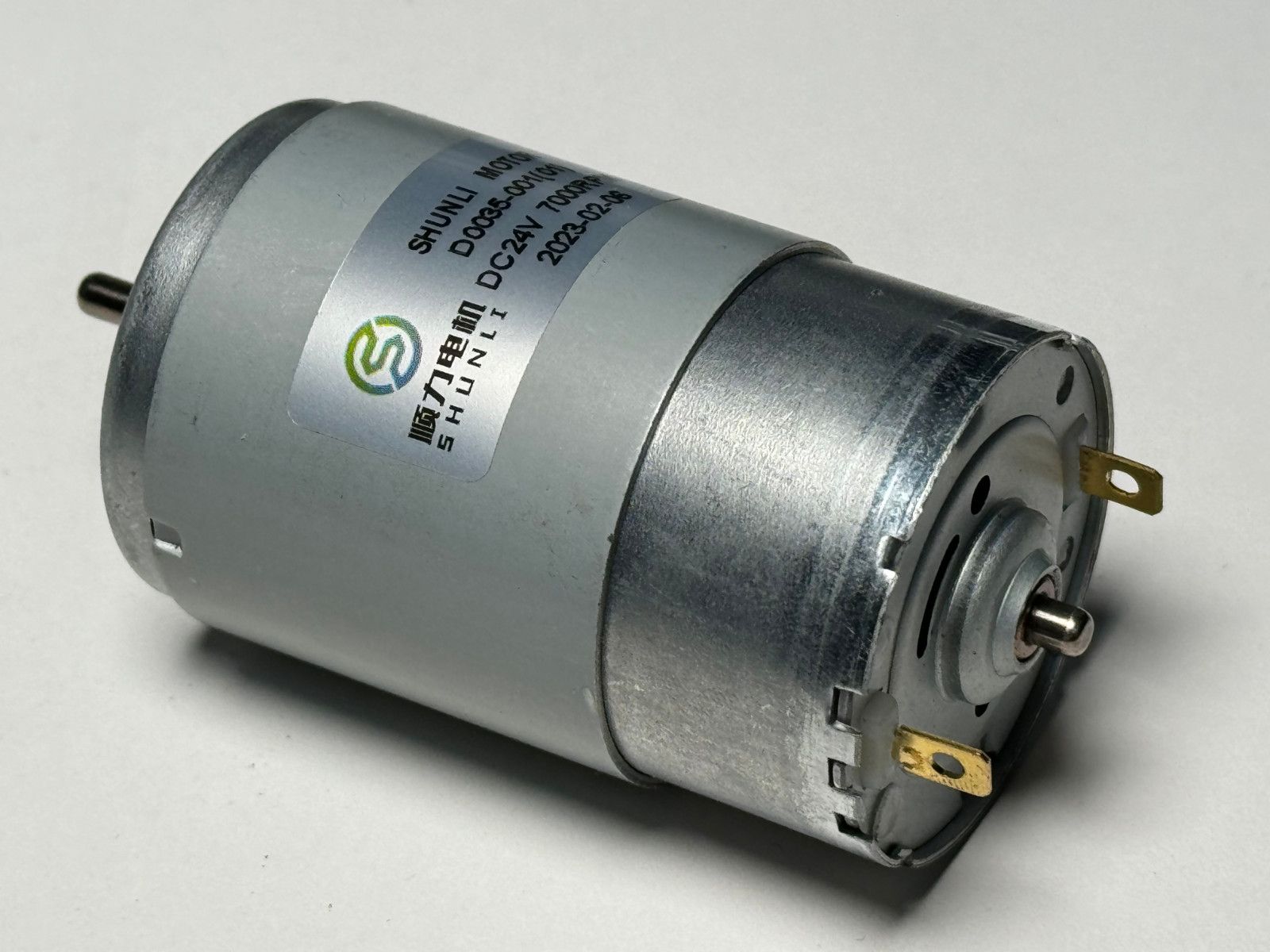
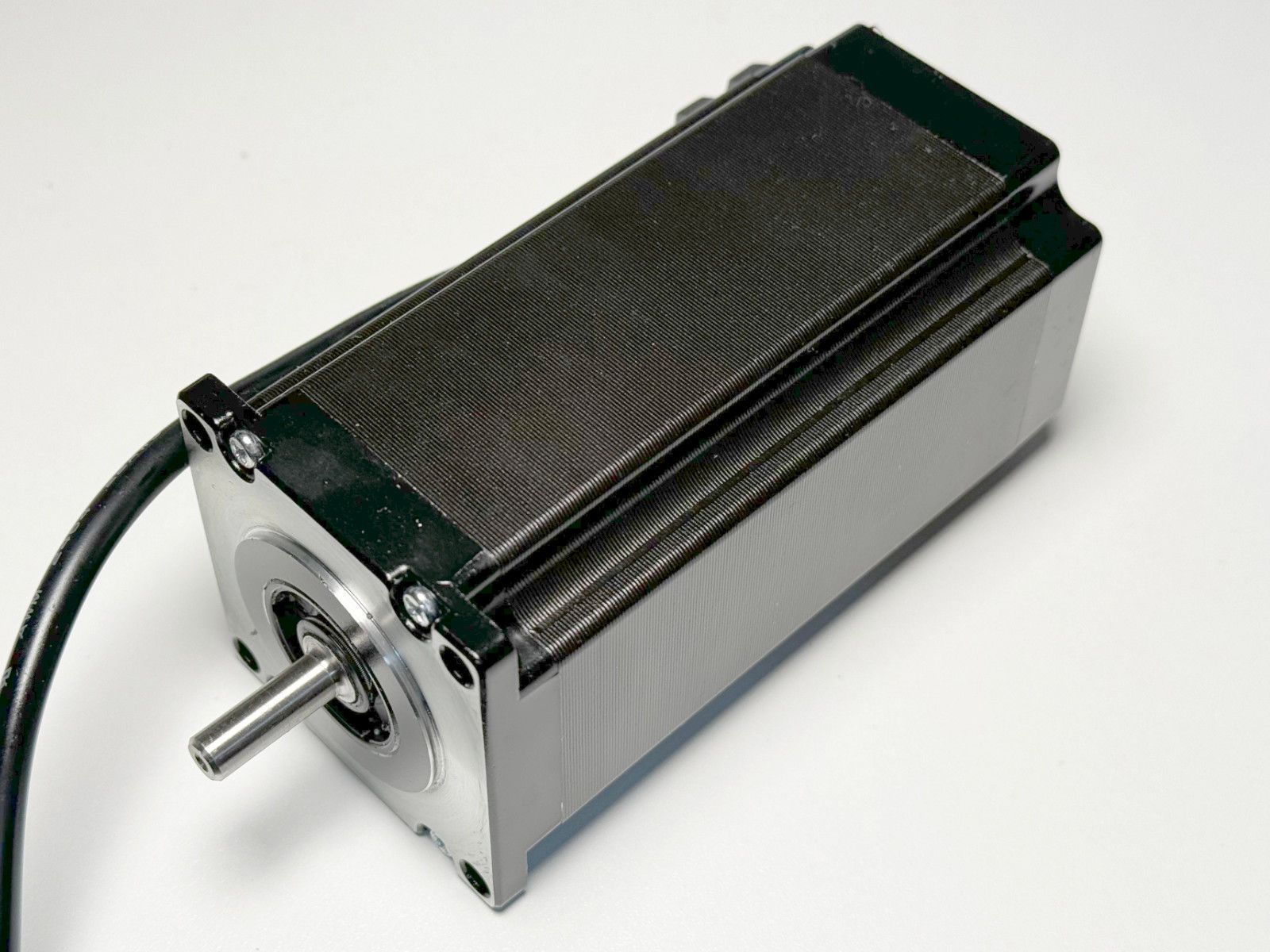
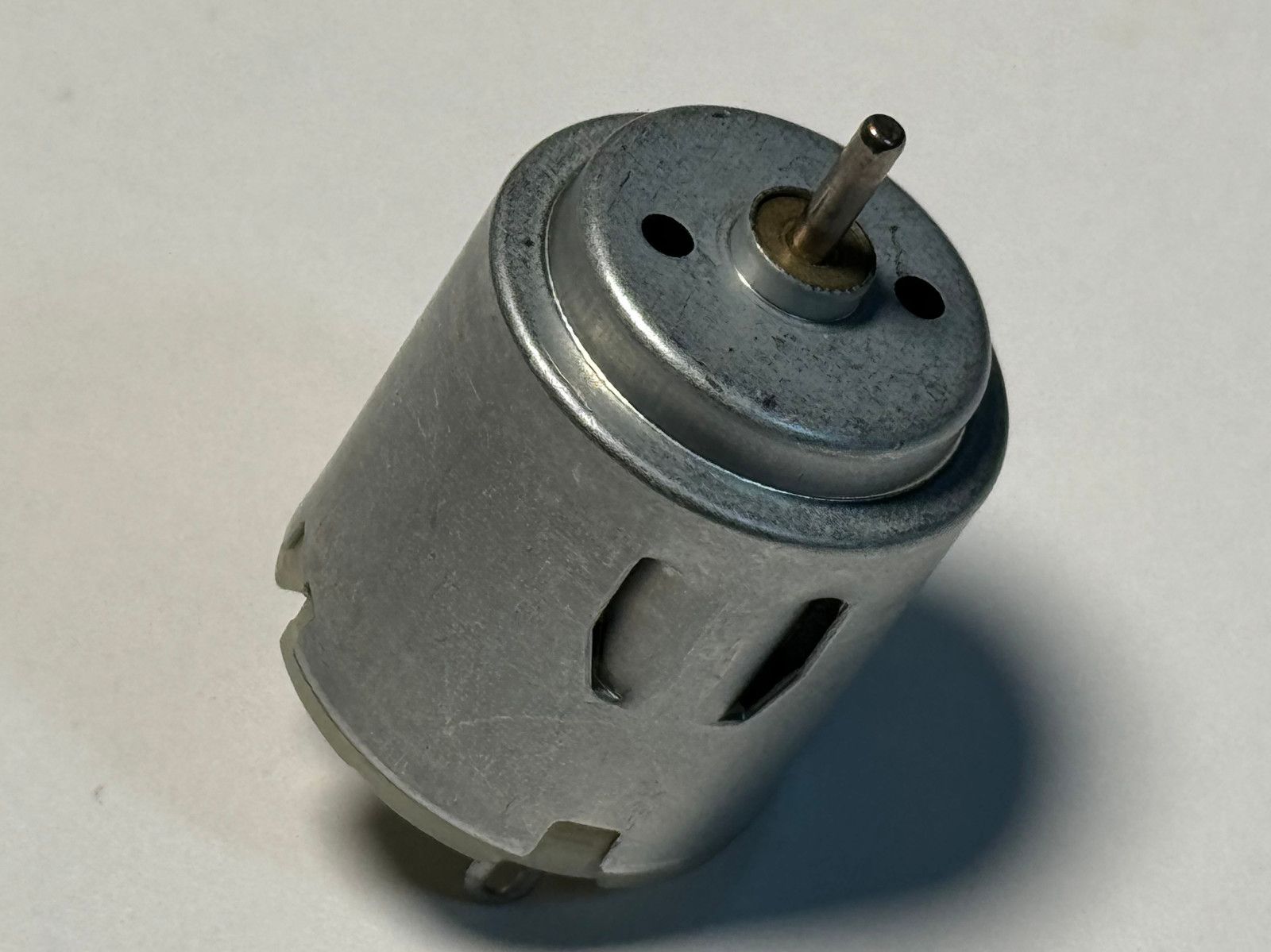
Figure 10:Upper Left- Nema 17 size stepper motors are common in consumer grade CNC electronics | Upper Right- Medium sized brushed DC motors are often found in cars and consumer appliances | Lower Left- Larger stepper motors are used in CNC milling machines and industrial automation | Lower Right- Tiny brushed motors are used in toys and small consumer products
Sensors
Though electric motors generate torque, producing raw torque alone is often not enough for an actuator to perform a task; sensors allow monitoring and control of an actuator's position and velocity.
Switches are a basic but extremely common method of sensing an actuator's position. They can be used to detect when an actuator is at one end of its range of travel.
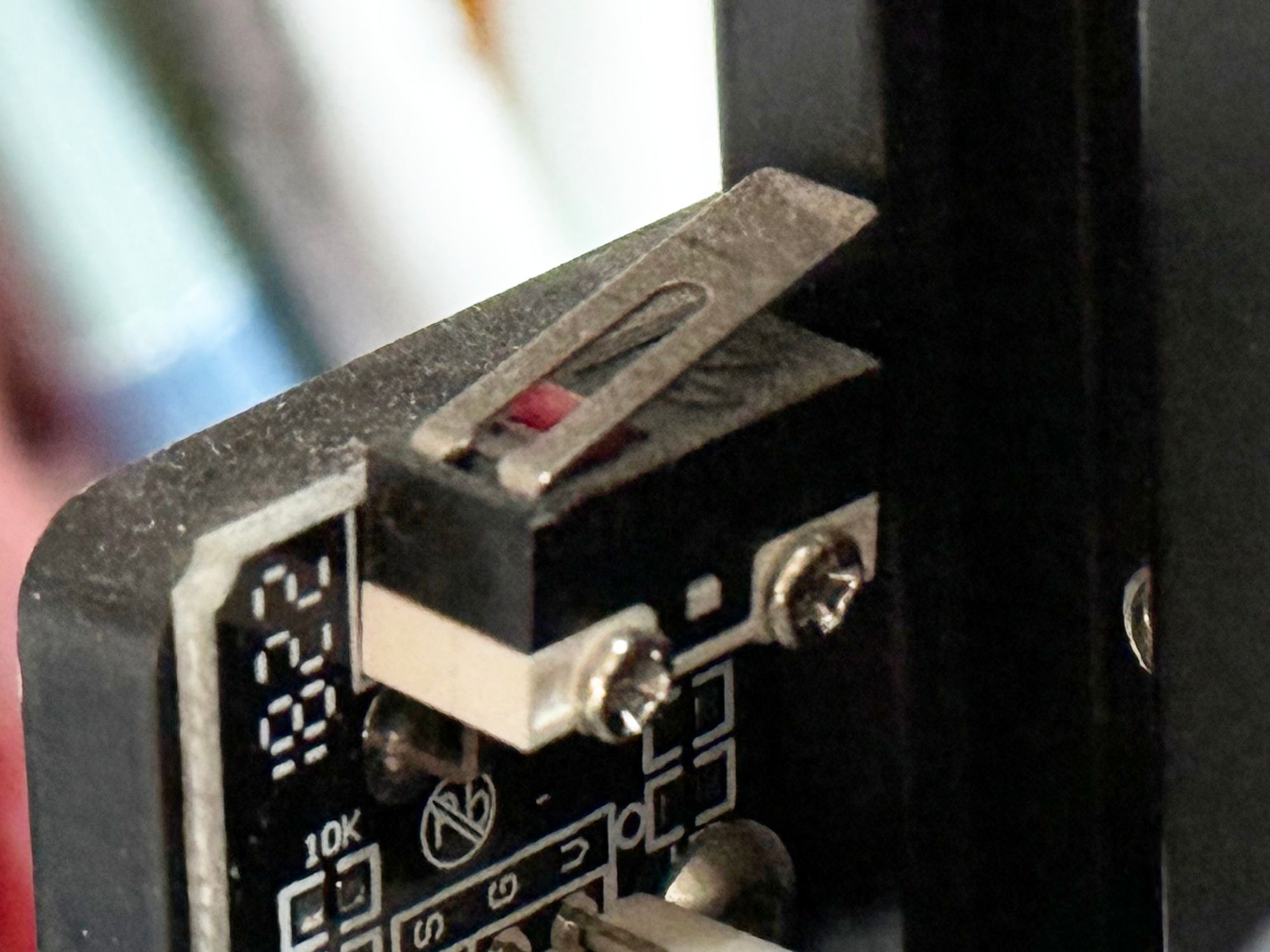
Another common position sensor are encoders. Encoders sense an actuator's position without inhibiting motion. Encoders can also be used to estimate velocity by counting the position change over a period of time. Acceleration can also be estimated by counting the estimated velocity change over a period of time, however, the estimate quality degrades rapidly with each derivative.
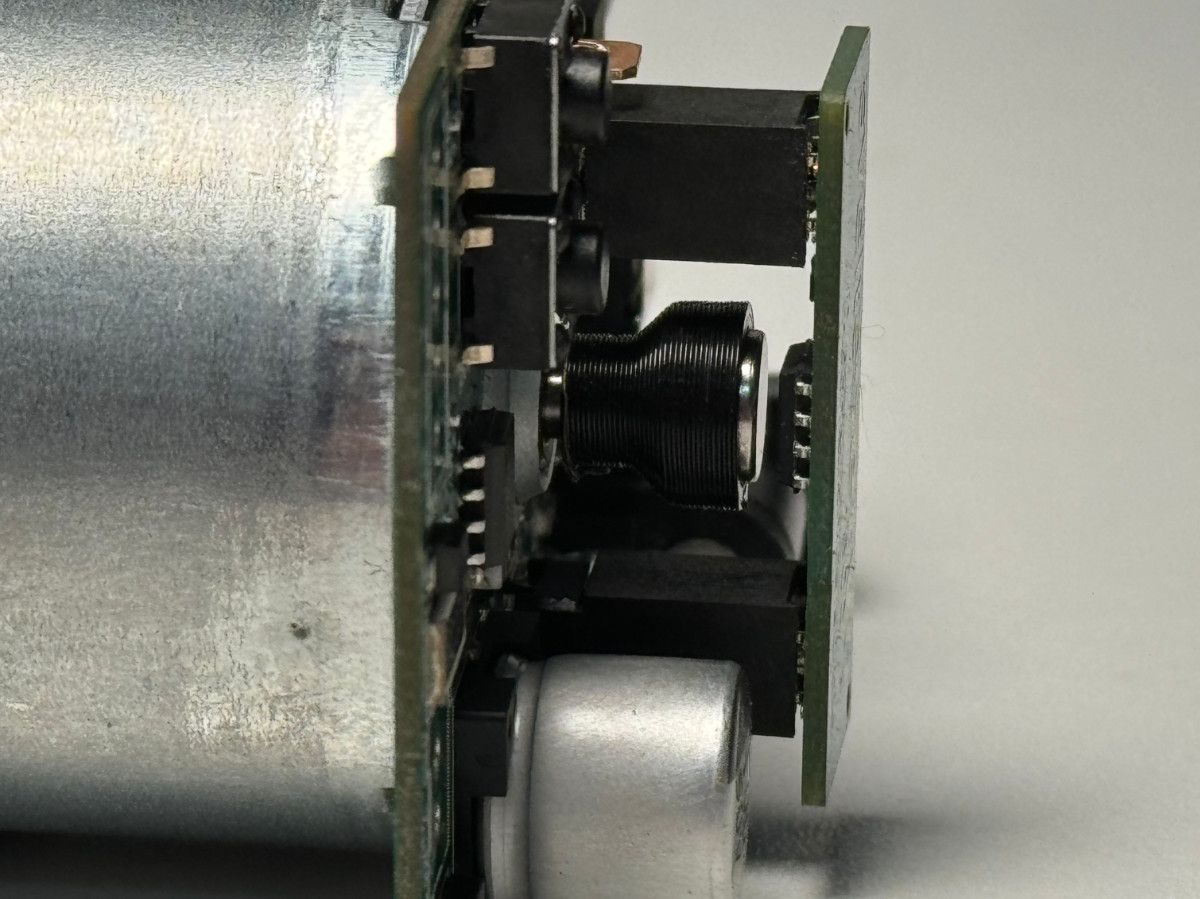
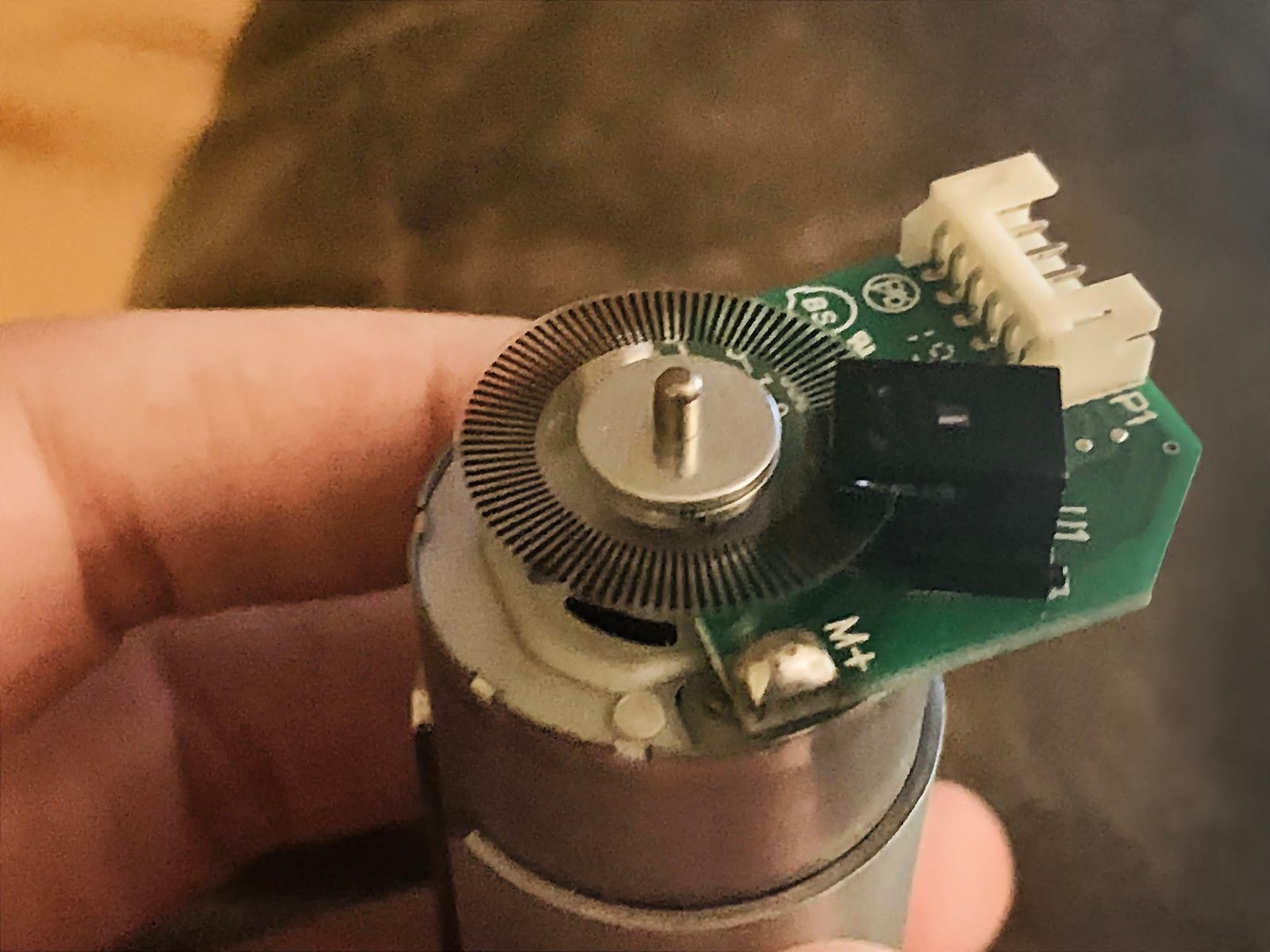
Figure 12:Left- Magnetic encoders have become increasingly available to the broader market. Because they are analog, their accuracy is highly dependent on the quality of the sensor. | Right- Optical encoders are very repeatable but are susceptible to dust, dirt, and debris.
Range finding sensors such as ultrasonic (sound) and lidar (light) measure distances from the sensor to other objects without touching them. They are not as accurate as contact methods like switches, but they can measure over a broad range of distance.
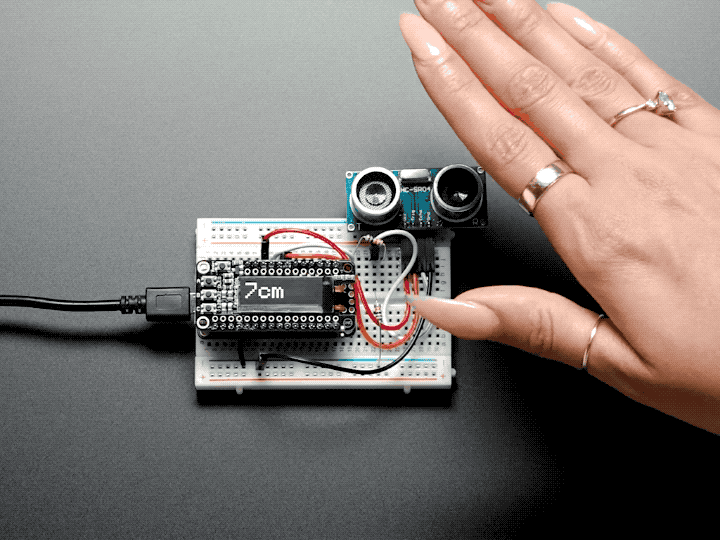
Accelerometers measure the acceleration imparted to the sensor, typically including gravity. This allows them to be used for global orientation measurement.
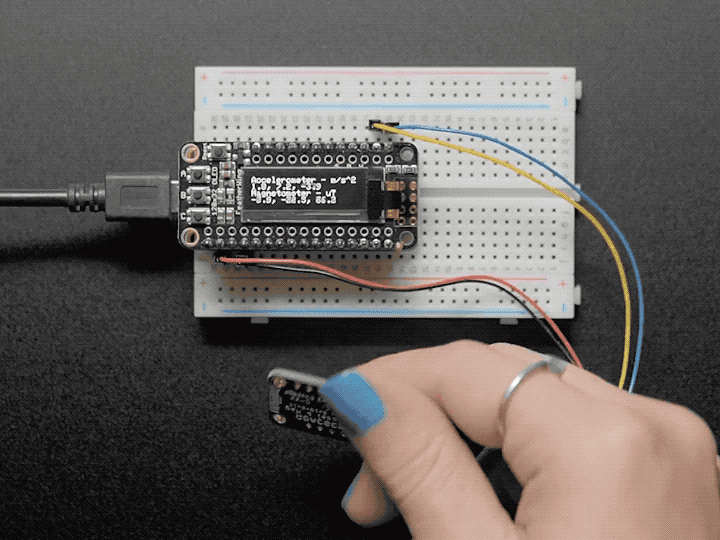
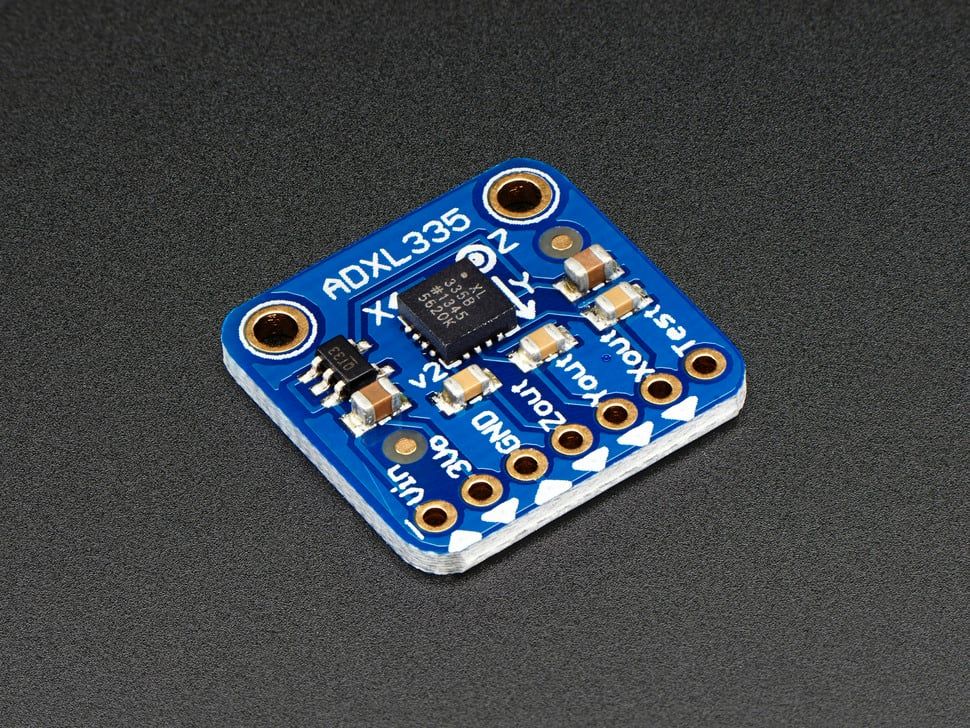
Figure 14: Left- Accelerometers can be used to capture motion and orientation. Courtesy of Adafruit, https://www.adafruit.com/product/4413 | Right- Accelerometer breakout boards provide an easy to use hardware interface for very small accelerometer chips. Courtesy of Adafruit, https://www.adafruit.com/product/163
Though cameras are in nearly all modern consumer devices, using them as a sensor requires a fast controller and specialty knowledge. While most sensors produce just a few sensor readings at any given time, each pixel in a camera is a light sensor producing data. A $1$ megapixel grayscale camera is considered low quality by today's standards but still produces $1,000,000$ sensor readings at a time (one for each pixel).
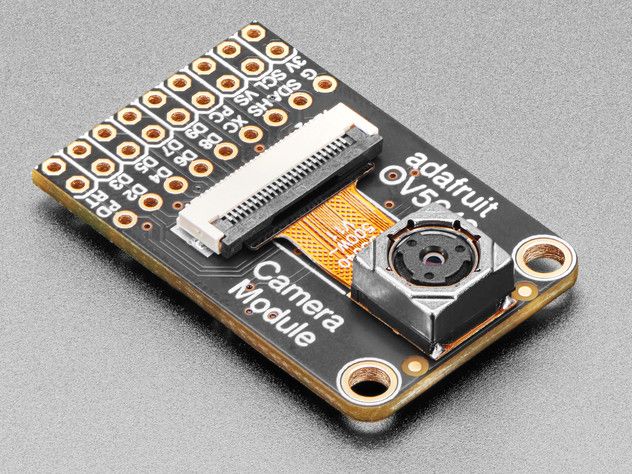
The possibility space for sensors is enormous. Other examples of measured quantities include voltage, current, temperature, pressure, humidity, strain, and infrared light. It would be impossible to cover them all here.
Mechanical Outputs
The mechanical output of a motor is the connection point between the motor and the rest of the actuator. The general slenderness of motor shafts together with the expense of shaft machining means that many motor shafts are poorly designed for transmitting the full torque capabilities of the motor.

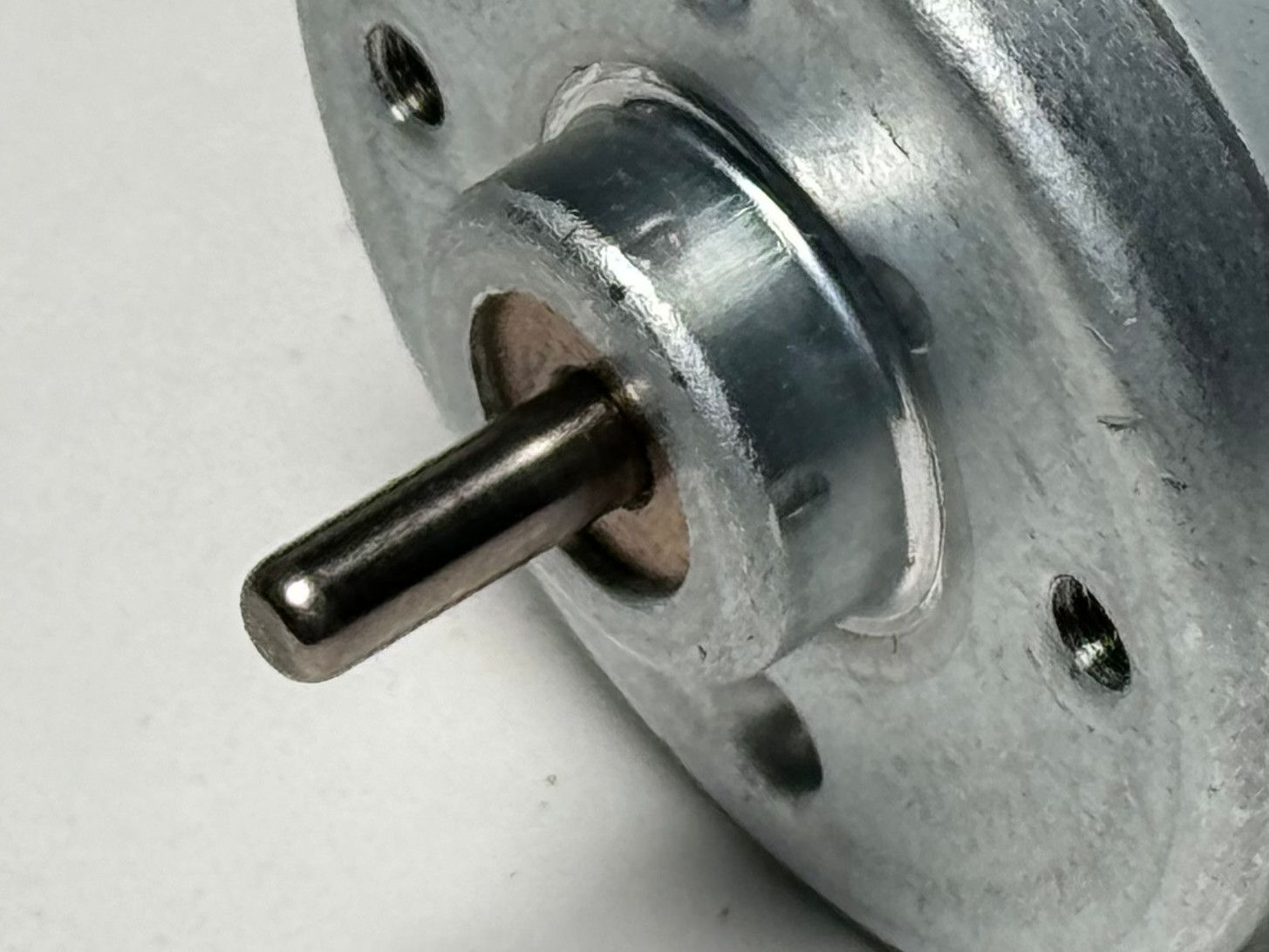
Figure 16:Left- Shafts with a flat on them, D-shafts, can be connected to other components with a set screw. | Right- Round shafts are cost effective but very difficult to attach well to components.
Motion Transmission (Gears, Belts, Screws, Pneumatics, etc.)
Motion transmission components transmit torque from the motor to the part of the actuator performing the task.
Synchronous transmission components (timing belts, gears) ensure that the motor rotation is synchronized with the entire mechanism. Asynchronous transmission components (pneumatics, hydraulics) don't guarantee the same.
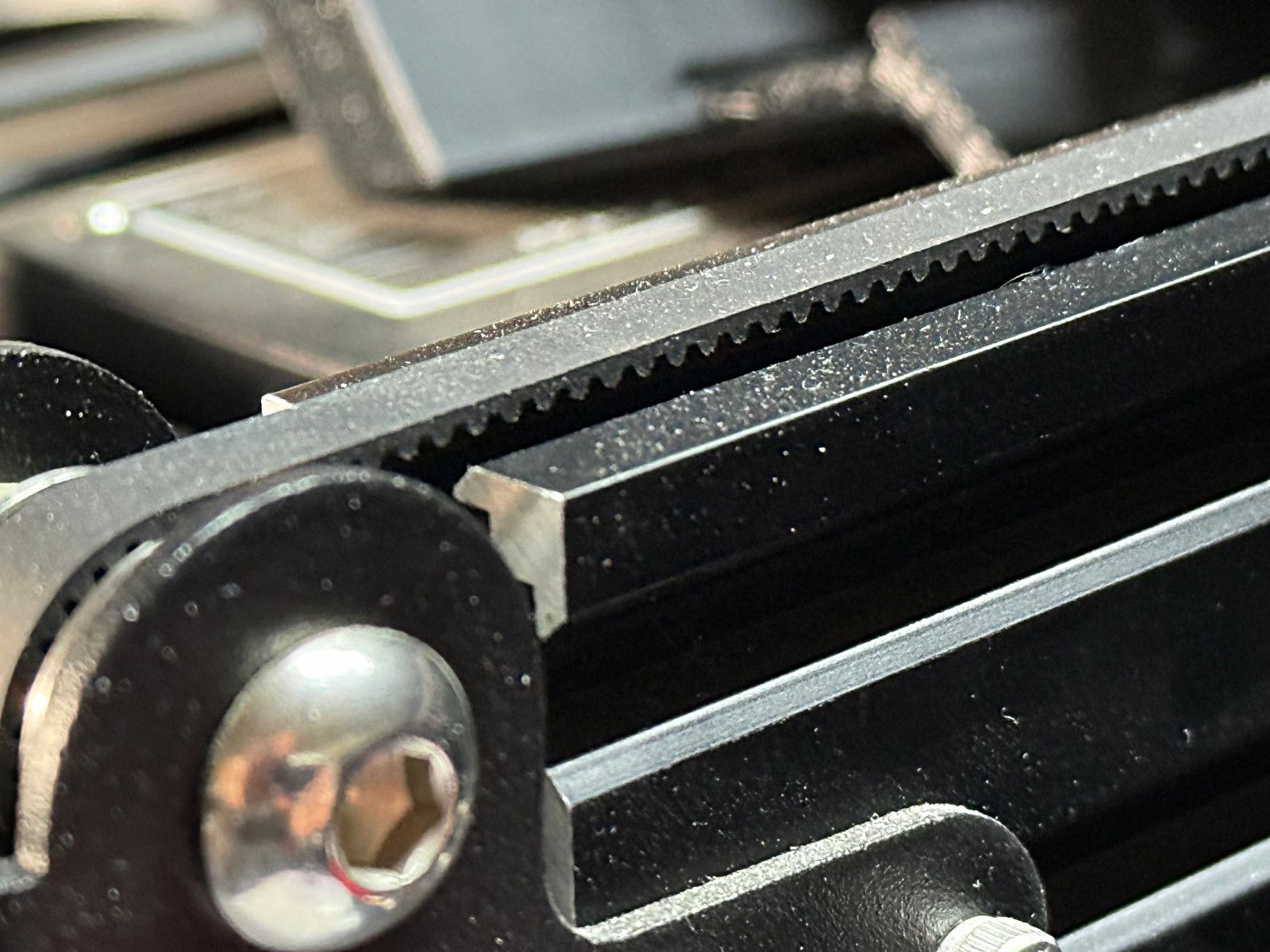

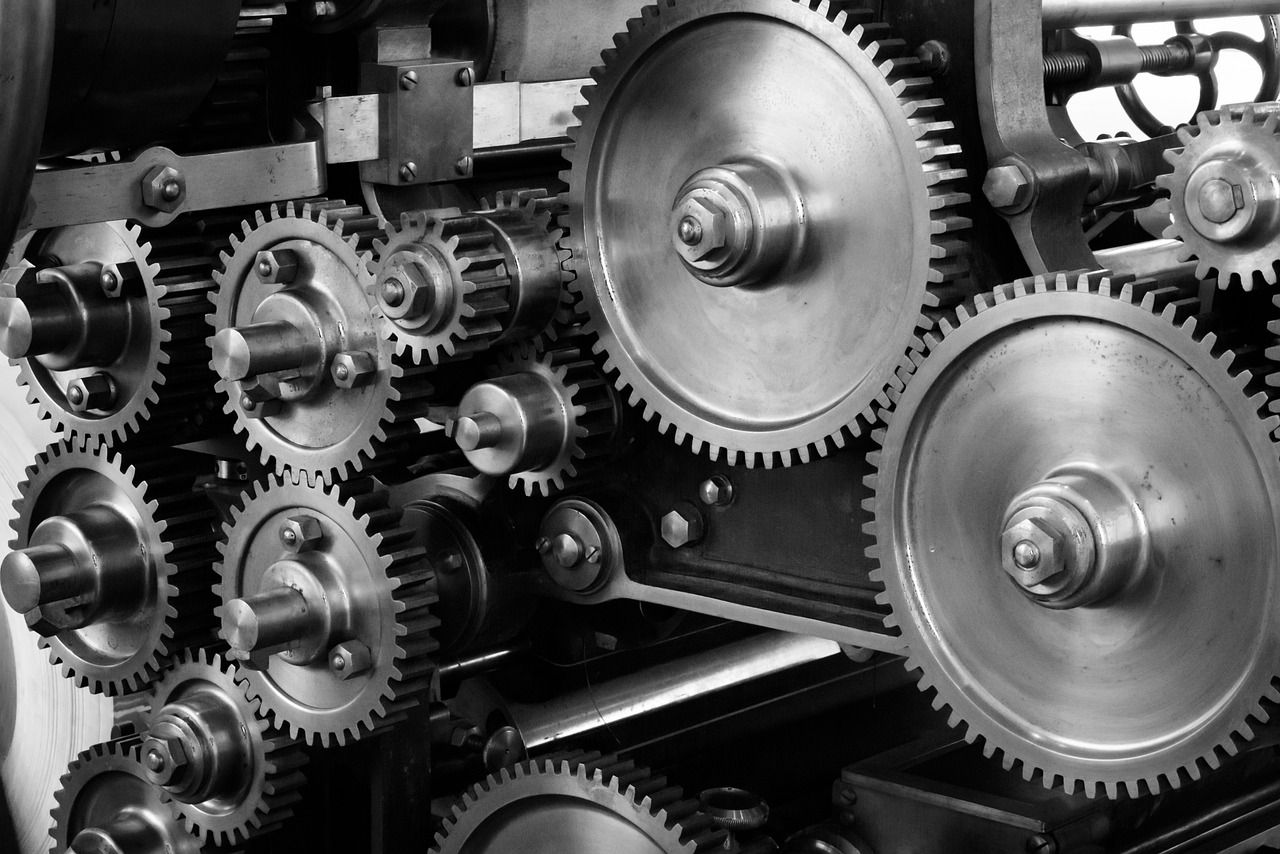
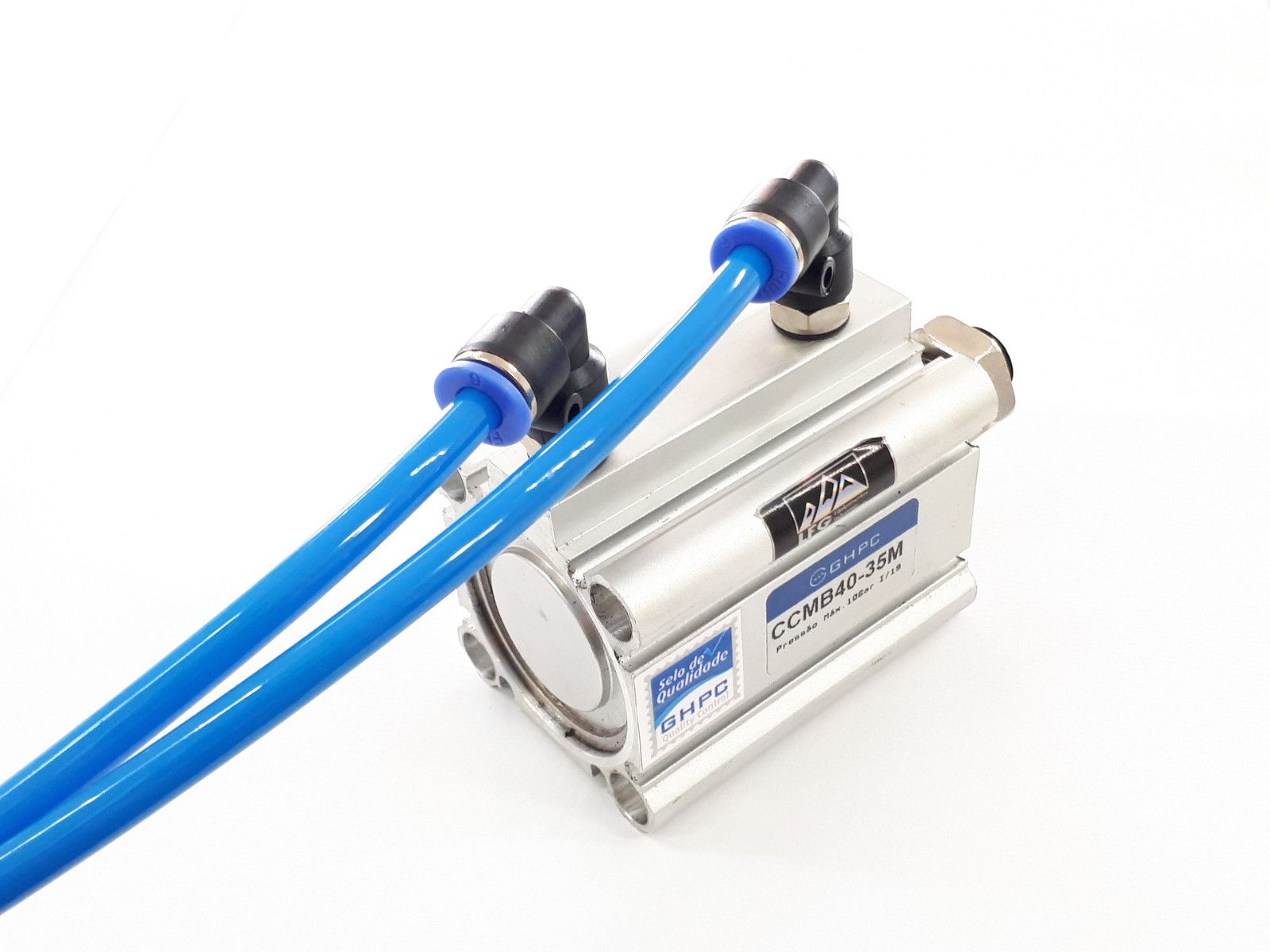
Figure 17:Upper Left- Timing belts are very effective at transmitting synchronous motion over long distances | Upper Right- Ball screws are extremely stiff and provide a lot of mechanical advantage | Lower Left- Gears permit for increasing speeds or torques in rotary applications | Lower Right- Pneumatics (compressed air) can be used to compactly transfer forces very long distances
End Effectors
An actuator's end effector is responsible for performing the actual task. Material cutting, depositing plastic, lifting boxes, looking pretty... these are all purposes of end effectors.
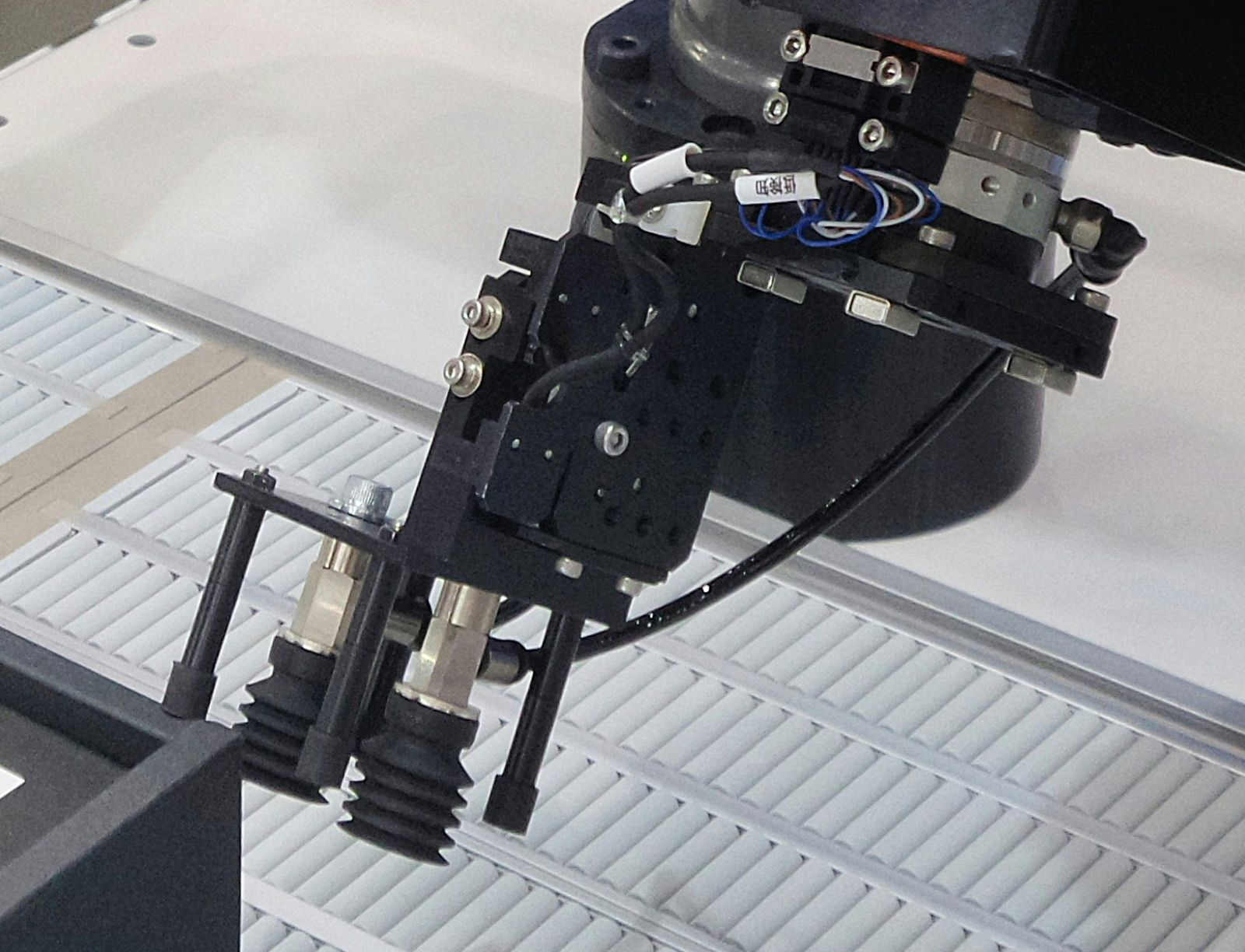
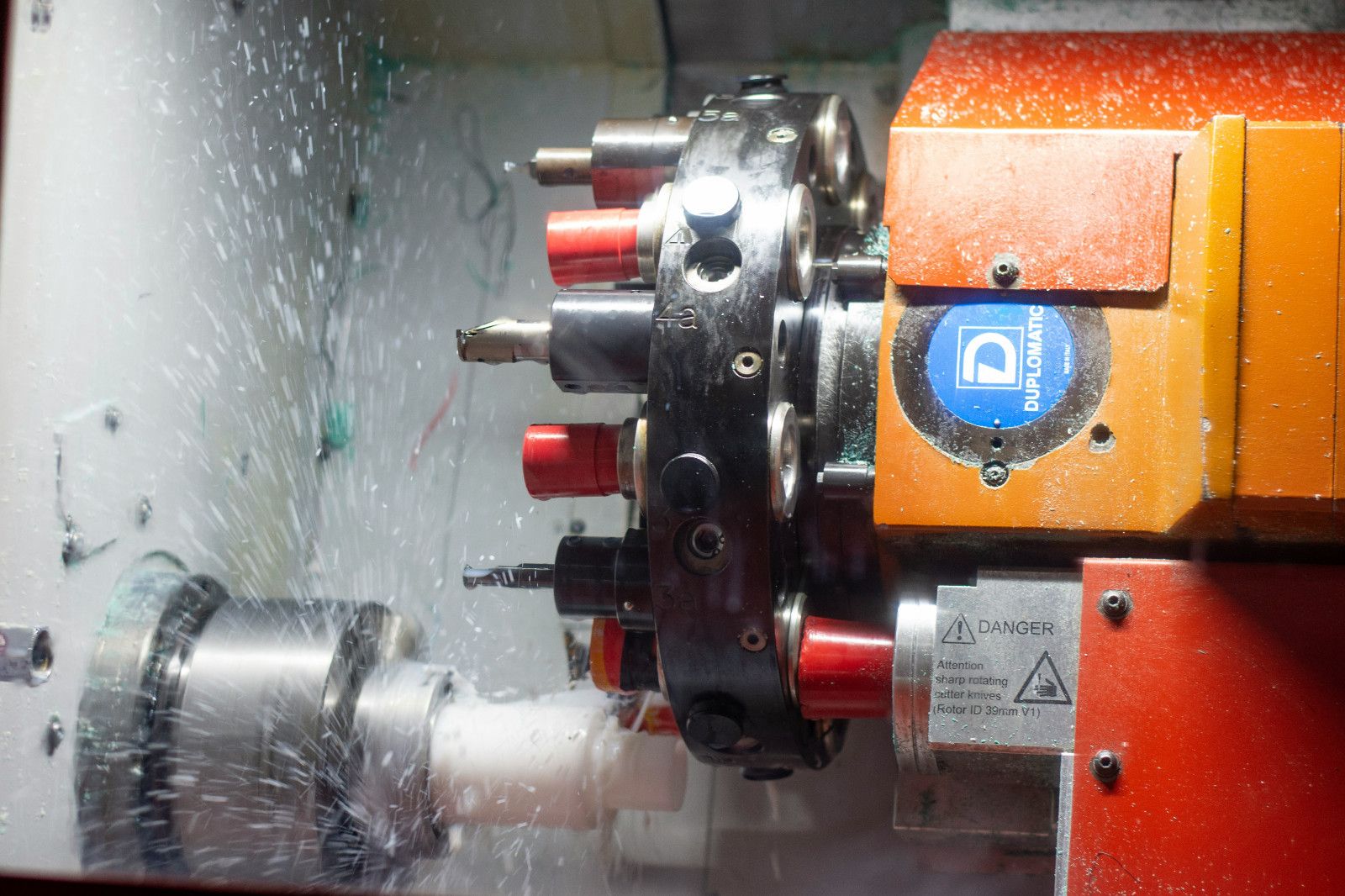
Figure 18:Left- Vacuum cups are common end effectors that help actuators to grip objects. Courtesy of Possessed Photography via Unsplash | Right- The cutters on CNC machine tools are end effectors. Courtesy of Afinis Group via Unsplash.